-
Currency:Localize your Content
You can set your preferred currency for this account.
Choose a Currency
Currency- CHOOSE YOUR CURRENCY
Update Currency
Changing Currency will cause your current cart to be deleted. Click OK to proceed.
To Keep your current cart, click CLOSE and then save your cart before changing currency.
-
Select Account
Switching accounts will update the product catalog available to you. When switching accounts, your current cart will not move to the new account you select. Your current cart will be available if you log back into this account again.
Account# Account Name City Zip/Post Code My Account
You are browsing the product catalog for
- Support
- Automation
- Resources
- Case Studies
- Christopher & Banks
Christopher & Banks
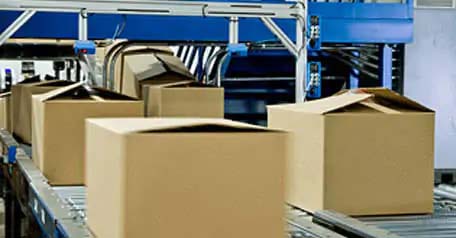
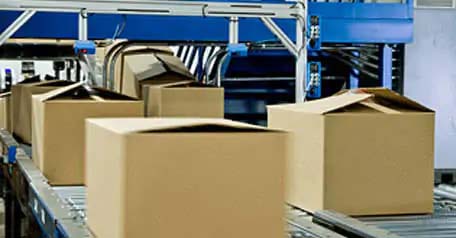
Christopher & Banks, a retailer of specialty women’s apparel with stores in 46 states, has a mission to deliver compelling, quality merchandise assortments to women ages 40 to 65 (baby boomers). The company places a high value on providing their “boomer consumer” customers with a positive brand and store experience. While many competitors are relying on steep markdowns to move inventory, Christopher & Banks strives to keep customers coming back with frequent additions of new merchandise on the racks.
To maintain the steady flow of product, the Plymouth, Minnesota-based company implements a disciplined inventory management process across its entire supply chain. The company receives 95 percent of its merchandise on a just-in-time basis, working closely with its suppliers to produce in-demand fashion items.
The Christopher & Banks 200,000-square-foot DC had been able to support quick fulfillment to its stores through cross-docking of full case pre-packs, but the transportation expenses associated with this method were cost prohibitive. Additionally, there was a strong desire to reduce transportation costs by re-packing items to increase box weight. The desire to repack a large percentage of merchandise strained the existing capacity and aging equipment. The facility relied on a very old, inflexible conveyor system, which was a source of chronic maintenance and other operational challenges.
Christopher & Banks finally found the solution they were seeking with Honeywell Intelligrated. Read the rest of the case study to learn how a well-defined project plan helped them to reduce expenses and improve safety, productivity, quality and customer service levels.
Copyright © 2024 Honeywell International Inc.
Maximum File Size
Maximum Files Exceeded
Due to inactivity you will be logged out in 000 seconds.